The Machine:
As promised here I start with technical information. If you goggle “CNC 3040” you will see that this is really a popular machine and there is a lot of information, especially in YouTube but it is hard to find a full operating manual of the machine and also the best settings for the controller software. Here I will try to summarize the most important aspects:
Where to buy it:
I purchased mine online via Ali Express but you can find it with similar price in Amazon or eBay. The title for the one I bought is: “3040Z CNC ROUTER DRILLING/MILLING MACHINE WITH 1.5KW VFD WATER-COOLING + 800W SPINDLE MOTOR ENGRAVER PROFESSIONAL”. I prefer not to share the links as they normally disappear when the machine is sold or obsolete. The vendor I selected offers free shipping from USA with no custom payments and price was the same of other alternatives. Below I copied the specs from the Ali Express vendor page.
3040z tri-axial engraving machine specifications:
Effective working travel | 410(X)mm*290(Y)mm*75(Z)mm |
Shape dimension | 665*525*465mm |
Max.thickness of the materials | 90mm(the distance between Z axis and the bottom of the working station) |
Max. work piece dimension | 390mm*290mm |
Work table dimension | 560mm*360mm |
Frame materials | 6061 aluminum alloy/ 6063 Industrial aluminum |
Driving units | X axis 1605 ball screws | |
Y axis | NEW 1605 ball screws |
Z axis | NEW 1605 ball screws |
Sliding units | X axis Dia.20mm chrome plate shafts | |
Y axis | Dia.20mm chrome plate shafts |
Z axis | Dia.13mm chrome plate shafts |
Stepping motor type | 57 two-phase 2.5A ,super-low noise ,NEW |
VFD Power | 1.5KW VFD,NEW |
Principal axis collet | ER11 / 3.175 collet or 6mm |
Spindle speed | 24000rpm/min (PWM steeples speed regulation) |
Empty line speed | 0-4000mm/min |
Resetting accuracy | 0.05mm |
Engraving accuracy | better than 0.04mm (has been tested) |
Spindle precision | radial run out 0.03mm |
Control unit | tri-axial one-piece drive + ring variable power + PWM speed |
Carving Instructions | G-code/.nc /.ncc/ .tab/ .txt |
Communication interface | through parallel connection with computer |
Software environment* | Windows 2000 / xp |
Carving speed | 0-2500mm/min (different materials differ) |
Machine weight | 46KG |
*Please see below for additional software information
I copied the picture below from the Amazon.com page as it has a full description of the components. The machine from Amazon.com is more expensive than the one I bough.

The software:
In order to run the machine it is necessary to have a software to translate the milling commands to electrical signals so the motors can move to the correct position and speed. The universal command language for CNC machines is the G code (http://en.wikipedia.org/wiki/G-code)
For this machine I use a very popular, powerful and inexpensive software: Mach3. In theory the machine comes with the software and the license. Mine came without it and the vendor send me a link to download it. I found that the version and the license in that link is outdated so I decided to buy the license for $175.00 directly from the software developer. And I did the right thing!
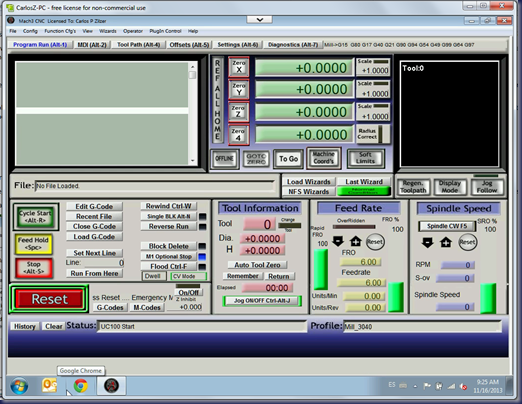
Mach 3 was originally developed to use as I/O port the parallel printer port in the PC, after the introduction of USB and Ethernet this port disappeared from all the laptop computers and is basically discontinued and difficult to find the expansion board for desktop computers. Also the old software doesn't run in Windows 7 or above.
The new versions of MACH3 can use what they call “Plugins” to be able to use special developed “Motion Controller Interfaces” that are basically USB or Ethernet converters to parallel printer port. Be aware that low cost USB to parallel port converters will not work and they are not fast enough to process and buffer the high speed pulse commands to the stepper or servomotors of the machine. The Plugin page of the Mach3 site lists all the plugins available and you can download there the drivers for these devices. I Selected the UC100 USB Motion Controller and bought it from eBay (CNC USB CONTROLLER for Mach3 Smooth Stepper Motion Control , UC100) for $150.00
Important Data to know before starting:
Whatever controls software you will use (I use Mach3) there is important data you need to know in order to properly setup the machine:
Here I am sharing PrtScn of the setup pages of Mach3 for my machine, but you need to check with the vendor the exact data of your machine. It seems that the CNC 3040 is built by different companies and the ball screws and stepper motors can change from vendor or manufacturer.
I setup my machine in metric units but this is only for Motor/Screw ratio. The G code and the postprocessor takes care of the working units via the instructions G20 and G21



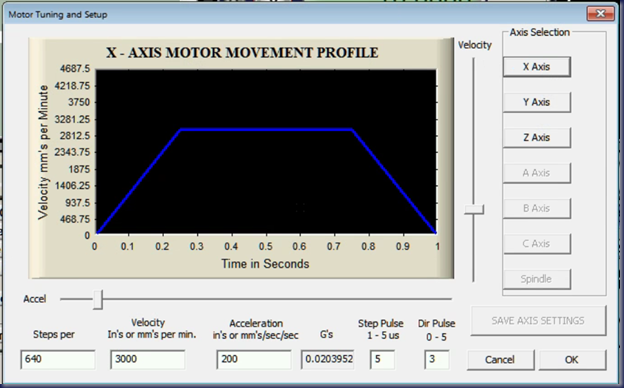


I think this is enough for now, I will continue with more technical information in future posts.